Introduction
The company approached us when their 30-year-old static compactor became too unreliable to continue using. We visited the site to have a look at their current setup, something we do regularly. They had a dock-loaded setup with a walkway, which was as old as the compactor and needed replacing as well.
The Challenge
This was a challenging build in almost every aspect. To start with, the static is located down a narrow back alley with a one-way traffic flow in place. The transport vehicle is too large to fit down the alley, and the entrance is along a busy road. There is also a choke point next to the compactor's location that reduces the width further, such that a large transit van is the widest vehicle that can pass.
The walkway and the static would be too big to safely transport on our vehicle as one unit, and they would be too large to fit through the alleyway.
The walls surrounding the dock are covered with air conditioner units and other wall-mounted equipment, meaning limited space for securing the walkway as well as manoeuvring the equipment into place.
The Solution
At the start, our mindset was to create a flat-pack system that could be built on-site. This would help us solve many of the transport issues and help us move it through the alley more safely. We planned to take our forklift truck to the site and park the main transport vehicle at the wrong end of the one-way system, which was down a quieter side road, and temporarily close the entire alley while everything was moved into the space. We discussed this with our partner, and they were happy with this plan.
We sent an engineer to the site for a second time to get precise measurements and photos so we could create a 3D render of the environment and all obstacles.
With the 3D environment created, our designer added the static compactor to it. The main chassis was a standard SC3000, and a chute was built to the height of the dock, then a walkway was created to connect the dock to the compactor.
Once the rough design had been created, our designer and an engineer reworked it, adding the hardware to make it flat-pack and all the connectors and anchoring points.
As with any project of this nature, we got our partner's feedback on the design, and once approved, we sent off the order for all the parts we would need.
When we had built, bolted, or welded everything together, our partner asked if they could send a couple of representatives up to have a look and to check out our workshop. We enjoy showing off our team and the workshop to visitors, so we organized a day for them to visit and showed them around. The reps were happy to see how everything was shaping up.
Key Benefits
We expect them to notice very little difference in the day-to-day costs as they already had a compactor on-site. They were getting an average of 4 tonnes per uplift. We expect that with the type of waste they are filling it with, they will likely get closer to 4.5 tonnes per uplift. The cost-saving that they will notice is the reduction of maintenance and breakdown costs.
Road Ahead
We will be servicing this machine and the RotorPac on-site twice a year so we will be inspecting it frequently. We have been communicating regularly with the team that fills the compactors for their feedback. At the time of writing this, we have moved the skip locators so they position the skip better for the new compactor.
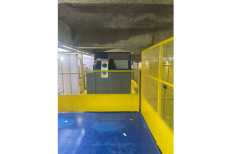
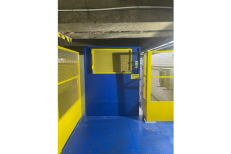
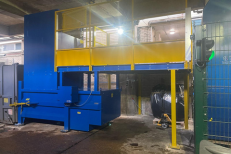
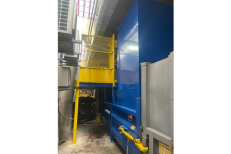