Welcome to the July edition of Compaction Catch Up, our monthly update on how the business is doing. We aim to show off our production capabilities as well as our superb team.
- Our colleague Oliva from the Pearce Group side of the business got married to her partner Ron at the beautiful Micklefield Hall in Rickmansworth. We've had to wait for them to get back from their honeymoon in Sri Lanka and the Maldives to see the photos!
- Don't they both look amazing!
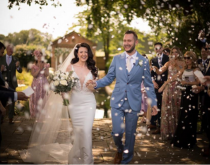
- We had another Toolbox Talk turned BBQ this Month, we are hoping that every future Talk is done over a BBQ.
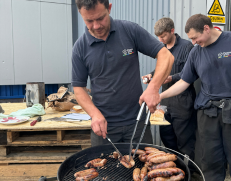
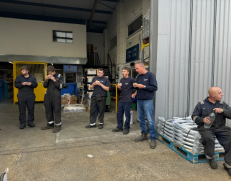
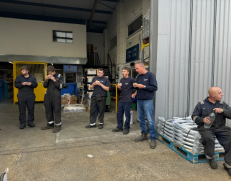
- We had a bit of an unusual request from one of our trade partners for a MC14BL Mobile Compactor with a Bin Lift... but without the Bin Lift. The site already had a mobile bin lift in use. Our hand-fed MC14 door and ram placement would not have been suitable for a mobile bin lift, the easy solution was a slightly modified MC14BL. Mark had to do some modifications to the design such as removing the bin lift and making the door opening at the same height as the mobile bin lift. Manufacturing for this machine will begin shortly.
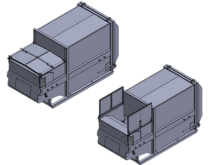
Not so many bespoke machines this month
- Our engineers have serviced 132 balers and compactors.
- We installed 18 compactors and balers, across 15 sites.
- We did 2 LOLER inspections
- And ran 6 training sessions.
- We are looking at expanding our team further, we need another Welder, Paint Sprayer, Bookkeeper/ Finance Assistant and a Field Service Engineer based in the Horsham area. If you are interested or know of any suitable candidates for any of these roles please email compaction@pearce-recycling.co.uk.
- We have taken on a temporary team member in the OPs team to help with digitising of customer files as we have stalled on this project with how busy we have been. She is with us for a month between leaving school and starting college in September.
- The workshop has started building the twin SC3000 Static Compactors with an inbuilt weighing system for a shopping centre in the Midlands. Each shop will have its own bins and will need to scan the attached barcode to operate the compactors. This will allow for a better understanding of volumes and the sources of waste for the facilities managers.
- This is the first time we have used this type of weighing system so we had an engineer from the weighing system manufacturer in to help us install everything correctly. As well as give our engineers some insight into maintaining the system.
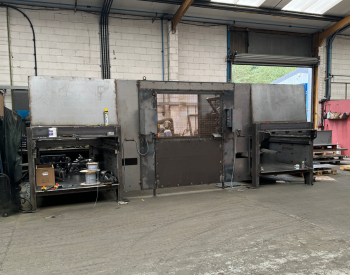
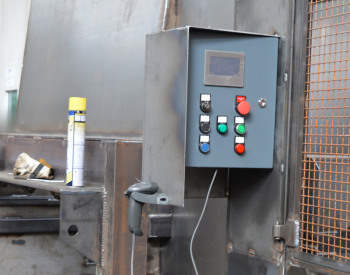
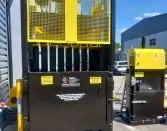
two more balers went out with brand colours, a striking combination of yellow and black.
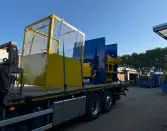
A standard SC3000Bl with a safety cage for one of our trade partners.
- One of the sites we have worked with for a number of years was looking to upgrade their waste management equipment. Their previous machines' placement had made their power leads into trip hazards so were looking for a better way to manage them. Our simple solution was to add a series of hooks to the underside of the compactors to keep them off the floor and no longer a trip hazard. And the hooks remain in the footprint of the compactor so won't cause a problem for shins!
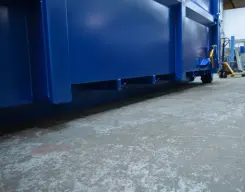
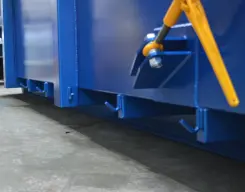
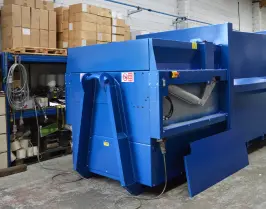
One of the compactors with hooks for the power lead also had a hydraulic lid fitted.
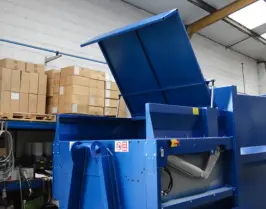
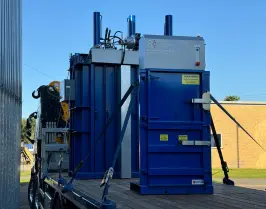
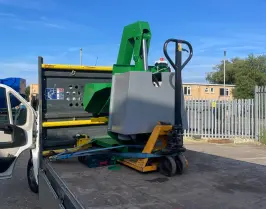