Introduction
Our Waste Management Specialist Tommie Coll visited A1 Bacon to understand the company's needs and advise on the best available options. On this occasion, a standard MC32W Wet Waste Mobile Compactor would have been too large for the available space. However, the company required maximum capacity, being a busy site with daily uplifts not being the optimal choice, The best option was to create a bespoke mobile compactor designed around their needs.
While our Waste Management Specialists excel in their field, they are not engineers. In this case, an engineer's expertise was necessary due to the tight spaces on site for manoeuvring the compactor and truck, as well as determining the compactor's placement. Steve Mason visited the site, met with the management team to discuss their requirements, and obtained all necessary measurements.
The Challenge
The company sought ways to reduce disposal costs for scraps and other rubbish while maintaining a streamlined waste management process. They faced limitations in space for accommodating a compactor, with height, width, and length constraints. Additionally, the compactor needed to be compatible with standard waste collector trucks.
The Solution
We developed a bespoke mobile compactor based on our MC32W Wet Waste Compactor design. We reduced the height by 500mm and slightly decreased the width.
Mobile compactors are typically transported in one direction, requiring only one set of rear rollers and a front hook for lifting. For this compactor, we installed an additional hook at the rear and corresponding rollers at the front, enabling backwards pulling for transportation.
To ensure compatibility with standard collection vehicles, we modified the chassis accordingly. Upon assembly, we tested the fit with a collection truck, making minor adjustments to ensure secure locking.
This compactor is designed to handle various waste types, including food and general waste. To prevent liquid buildup, we installed taps on either side near the rear door for periodic draining. We incorporated SmarTec to enhance compactor efficiency. Automated email notifications are sent to the warehouse management team and waste collectors at
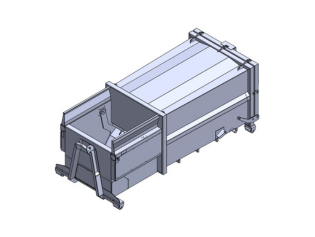
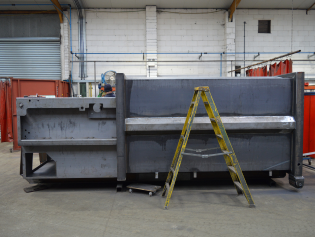
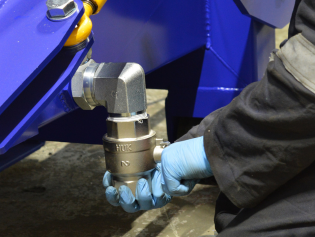
Key Benefits
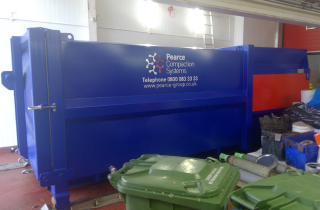
This compactor reduces waste management costs by minimizing uplifts and can be positioned near waste generation points, improving efficiency. Its extra rollers and hook facilitate easy movement, and the SmarTec upgrade ensures it is emptied only when necessary.
The Road Ahead
We will collaborate closely with the company to monitor uplift weights and gather feedback for potential design enhancements for future projects.
18/03/24: They found bags were occasionally remaining on top of the packer after the compactor had cycled so we adjusted the number of cycles from 2 to 5 remotely through the SmarTec, whilst we were on the phone with them. This didn't need an engineer to go to the site saving time and getting a problem solved almost instantly. After a couple of days with the new settings, there have been no reports of bags staying on the packer.